Our huge vary of products consists of PVC wall panels, outside wall cladding, waterproof flooring as an alternative to laminate or LVT, waterproof shower and toilet panels and far more. These embody cladding, small metal pins coupled with a ceramic mass, half-pipes and SiC tiles, in addition to numerous forms of coatings, including thermal spray coatings. Its characteristic feature is the sash bar down the middle of the window and black (similar to RAL 9005) metallic cladding coverings on the window and flashing which matches traditional buildings. The Independent Expert Advisory Panel additionally advised the department to determine a research challenge to test and enhance the proof out there on the behaviour of a variety of non-ACM materials used in cladding systems when subjected to fireside.
The course of is often used to create a protecting coating for elevated performance, as well as restore damaged or worn surfaces. Laser cladding permits extended life of apparatus and equipment by which elements are uncovered to corrosion, wear or impact. For instance, the construction gear trade applies this know-how to their products to increase put on resistance and maintain equipment in service longer. A high-energy laser is used as the heat supply in laser cladding. During the process, a surface layer is created by way of melting and the simultaneous software of virtually any given material.
The compromise between these competing calls for has produced wall thicknesses of ∼0.9mm in BWRs and ∼zero.7mm in PWRs. Laser cladding often involves covering a comparatively cheap substrate materials with a more expensive alloy that can improve the resistance of the half to put on or corrosion.
Zry manufacturing strategies now offer far better management of gaseous impurities than early fabrication technology, so the original reason for including tin is moot. Since tin is a substitutional impurity, its operate is to increase the strength of Zry over that of pure zirconium. 1.5% tin, and the balance being iron, nickel, and chromium.
Moreover, embrittlement owing to irradiation or temperature needs to be mastered so as to keep away from rupture in the reactor or through the back-finish of the cycle (handling, washing, and so on.). Cold-worked austenitic steels (with composition closed to that of the cladding) had been used first but at the moment are incessantly replaced by more swelling-resistant ferritic–martensitic steels (9Cr kind), in as far as the peak wrapper temperature, decrease than that of cladding, allows avoidance of thermal creep problems.
Cladding equipment is mostly designed to go well with a particular product or a bunch of products; this significantly applies to the items required for uncoiling of the strip and the feeding software. The material and floor of the rolls as well as their geometrical form (cylindrical or topped) are essential.

metallgeschottet adj
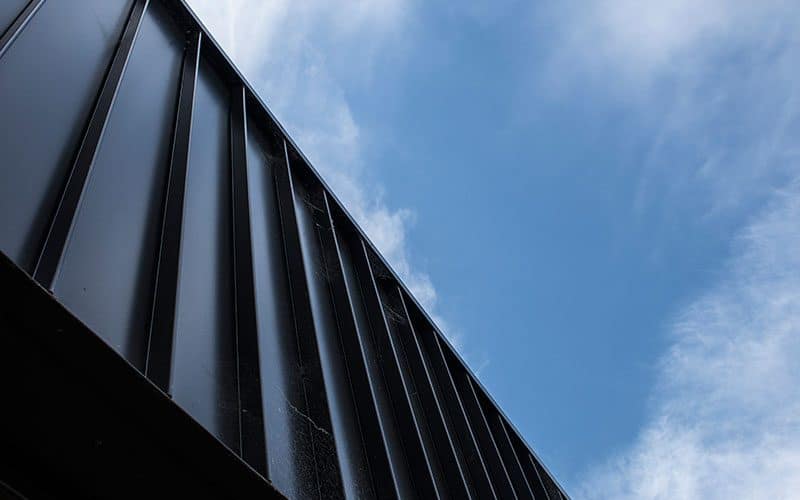
The compromise between these competing demands has produced wall thicknesses of ∼0.9mm in BWRs and ∼0.7mm in PWRs. Laser cladding usually involves overlaying a comparatively inexpensive substrate materials with a costlier alloy that may improve the resistance of the part to put on or corrosion.
Cladding permits the bulk of the half to be made with cheap materials, while offering the surface with fascinating properties associated with the more expensive cladding materials. Laser cladding has resulted in surfaces with superb end, good homogeneity, and very low porosity. Common supplies used for cladding embrace carbides, iron-primarily based alloys, nickel base alloys, and cobalt base alloys. Laser cladding is a process in which a metallic coating is applied onto the surface of an element using a laser as the warmth supply.
tube. Energy, from fission, is generated approximately uniformly throughout the fuel pellets. Heat is extracted at the rod surface by the coolant flow. The temperature at the hottest level, at the pellet centerline, is usually within the range 800–a thousand °C, relying on the facility stage. The metallic cladding is an efficient conductor, so the temperature rise throughout the wall is only some tens of levels.
In PWRs the closure of the hole between the pellet and the clad takes about one full energy year whereas the gap is maintained for a longer interval in BWRs. Due to the collapsible clad design of PHWRs, contact between the pellet and the clad is established right from the start of the life of the gas component. Laser coating or laser cladding can be used to regionally functionalize metallic elements. In this course of, an edge layer of sometimes zero.1 to 2 mm is applied to the part. The coating materials employed is both powder or wire, or utilized upfront as a tape.
Joining occurs constantly by local plastic deformation of the contact area (Ruge 1993 ) (see Fig. 1 ). Figure 6 . Schematic diagram showing the mechanism of the oxidation course of and the oxide movie construction on zircaloy. Figure 5 .
Applications for Surface seeMore Info Treatment
Zircaloys additionally suffer from bad creep charges. In contrast to surface-layer welding, explosive welding causes no change in microstructure, and corrosion resistance of the layers just isn't affected (Pocalco 1987 ).
Long-term, in-reactor, oxidation, and hydrogen decide up conduct of zircaloy-2 and Zr-2.5Â Nb stress tubes, showing parabolic and then accelerated linear oxidation and hydrogen pickup kinetics in zircaloy-2. A low and uniform price of corrosion and hydrogen choose up is seen within the in Zr-2.5Â Nb alloy. Differential swelling between cladding, wrapper tube, and spacing system (spacer wire or grids) can induce further stresses and deformations on these components and/or generate coolant flow perturbations in the bundle. These phenomena have been studied and have significantly proven that wires or grid supplies need to be chosen and specified to be able to minimize differential swelling.
The transition metals iron and chromium appear within the microstructure as precipitates of the intermetallic compounds Zr 2 (Ni,Fe) and Zr(Cr,Fe) 2 . These minor alloying components improve corrosion resistance to an extent depending on the dimensions of the precipitates. Laser cladding has been utilized to hardening of steam generator turbine blades and reached pilot production status [four ]. The blades had a machined pocket, into which powdered cobalt-primarily based metallic (Stellite 6) was fed forward of the laser beam.
With it, we process particular person parts in addition to collection elements, inner as well as outer contours, new and used components. Cladding in building is materials utilized over one other to supply a skin or layer and used to supply a level of thermal insulation and weather resistance, and to improve the appearance of buildings. Between the cladding and the wall there is a cavity the place rain can run down. Laser cladding with the aid of power-based or wire-formed filler supplies can be utilized for restore work, the applying of wear and tear and corrosion protection and the manufacturing of 3D components (additive manufacturing).
The graphite layer offers lubrication to minimize the mechanical interactions, and acts as a barrier against the migration of dangerous species to stressed areas of gas tubes. The original objective of tin in Zry was to mitigate the loss of corrosion resistance caused by pickup of impurity nitrogen during fabrication of the alloy.
The thickness of the cladding is a design parameter dictated by conflicting performance requirements. The impact of loss of metallic by internal or outer corrosion is much less important for thick cladding than for thin-walled tubing.
Once the pellet/clad hole is closed, any change in pellet dimensions causes stress in the cladding and the synergy between the stress and the corroding medium induces the SCC process. In order to prevent or decrease pellet/clad interactions, each mechanical and chemical, a coating of graphite powder is applied on the internal floor of cladding tubes.
Its commercial identify is Zircaloy, or Zry for brief. Zry is available in two varieties, Zry-2 and Zry-4. These two differ by minor changes in the concentrations of the transition metals (Zry-4 has no nickel). PWRs use Zry-four whereas BWRs employ Zry-2 as cladding and both Zry-2 or Zry-four for the duct or channel holding the gasoline-component bundle.
The soften layer is sort of skinny; for instance, when cladding an aluminum alloy it's about 0.5–fourμm (Kreye 1985, 1997 ). The dilution of the molten zones leads to plane or corrugated interfaces. During mechanical decladding, the gas assemblies are chopped and the gas core is leached with nitric acid, abandoning the undissolved cladding materials for disposal as a strong waste.
For the same external loading, the stress produced in the cladding, either external from the coolant or inside from fission-product swelling of the fuel, is reduced in proportion to the wall thickness. However, thick cladding is detrimental to neutron financial system, will increase the quantity of the reactor core, raises gas temperature, and costs greater than skinny-walled tubing.
tube. Energy, from fission, is generated approximately uniformly all through the gas pellets. Heat is extracted at the rod floor by the coolant flow. The temperature at the hottest point, on the pellet centerline, is typically within the range 800–1000 °C, depending on the power stage. The metallic cladding is an effective conductor, so the temperature rise across the wall is just a few tens of levels.
In PWRs the closure of the gap between the pellet and the clad takes about one full power 12 months whereas the gap is maintained for a longer period in BWRs. Due to the collapsible clad design of PHWRs, contact between the pellet and the clad is established right from the start of the life of the gasoline factor. Laser coating or laser cladding can be utilized to domestically functionalize metallic parts. In this course of, an edge layer of usually 0.1 to 2 mm is applied to the element. The coating materials employed is both powder or wire, or applied in advance as a tape.

Ceiling my review here Cladding
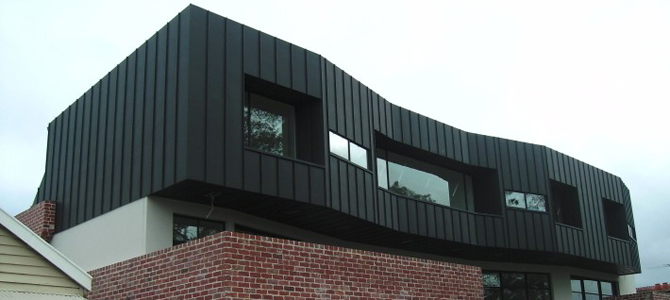
The filler material can both be equipped in powder kind e.g. as metallic powder, or with a welding wire. When laser cladding is carried out utilizing powder, the laser normally heats the workpiece with a defocussed laser beam and melts it locally. At the same time, an inert fuel mixed with a fantastic metallic powder is introduced. The metallic powder melts on the heated space and is fused to the surface of the workpiece.
Dissolved oxygen in PHWR coolant is managed between 10–50 ppb and it has been noticed that corrosion in each zircaloy-2 and Zr-2.5 Nb strain tubes rises to an exceptionally high worth at high oxygen concentrations. The BWR coolant often accommodates the next level of oxygen, sometimes 200–four hundred ppb.
As the oxide layer grows, the compressive stress on the outer layer of oxide just isn't sustained and consequently the tetragonal phase turns into unstable and transforms into the monoclinic phase. Such a change causes the formation of a fantastic interconnected porosity within the oxide movie which permits the oxidizing water to return in touch with the metallic surface. With the development of an equilibrium pore and crack structure in the oxide layer, the oxidation price effectively becomes linear, a characteristic characteristic of the publish-transition oxidation habits.
Its business identify is Zircaloy, or Zry for brief. Zry is available in two varieties, Zry-2 and Zry-four. These two differ by minor modifications within the concentrations of the transition metals (Zry-4 has no nickel). PWRs use Zry-4 while BWRs employ Zry-2 as cladding and both Zry-2 or Zry-four for the duct or channel holding the gasoline-element bundle.
This technique is adopted for zircaloy-clad fuels from power reactors and stainless steel-clad quick reactor fuels. Like the cladding , underneath the impact of neutron flux the hexagonal wrapper tube undergoes change. Geometrical changes, induced by swelling and irradiation creep (underneath the impact of dynamic sodium pressure), concern size, throughout-flat dimension, and, for subassemblies placed in the periphery of the core, bowing (differential swelling induced by differential flux and temperature between reverse faces of the wrapper tube).